私どもではある程度(体験的)な話は出来ますが、データーで表せと言われればお断りしなければならないほど現実的にはまだこれからの課題であって、おそらく結論が出るのは相当先の話となるでしょう。
実際あった話なのですが「以前、実施した試験では何も腐食は観られなかったが今回の試験結果をみると腐食が激しく試験機がおかしいのではないか?」と言う様な話を聞く事があります。確かに試験槽の中で部品のセット状態により若干ですが腐食度合いが違う場合がありますが、それより大きなファクターとして次のようなことがあげられ、上記のような質問が聞かれるものと確信致します。
メッキサンプルは同じロットの中でも各々腐食の表れかたが違います。ましてロットが違い製造日が数ヶ月も違う様な物ではとても比較にはならないほどです。ですから、現行の試験はあくまで比較試験と考え、前に実施したからと言って安心していないで品質管理の一貫としてガス腐食試験が有用であると考える事が重要です。自然環境中には微量ですが色々なガスが含まれ、場所によってかなり高濃度の腐食性ガスが存在したりしております。また密閉された物のなかにも発生要因が存在すれば密閉の意味が無くなってきます。
始めにガス腐食試験が評価として適していると書きましたが、シングルガスとミックスガスではそれらの結果は大分違ってきます。
一般に銀、銅などは硫化水素が強い腐食性を持っておりますし、金メッキなどは水分と一緒になって酸性となる二酸化イオウ、
二酸化窒素などの使用が推奨されています。しかし、実際の環境では濃度はかなり低いものの窒素酸化物、二酸化イオウ、
硫化水素、塩素、アンモニア、ホルムアルデヒドなどが存在し、また周辺材料などから発生しています。
ですから、シングルガスでの影響を充分把握した上でバテル規格などの低濃度3種混合試験などを実施すれば一般自然環境下の使用に対して特に再現性に優れていると思われます。
しかし、中には特殊な条件下で使用される部品もあり、試験温度が高かったり濃度が高かったり様々です。
同時に接触機構部品は本来機能部品ですから使用環境ほか各々の特性からガスの作用を受けやすい物も、そうでない物も存在します。ですから、そのような部品の接触信頼性に付いて加速係数を論じるのはそれほど簡単ではないという事がおわかり頂けると思いますが、各方面で実施検討されている事例などを含め、述べたいと思います。
まず基本データーを取る為に一般的には実際の部品を屋外、屋内など各場所に設置、少なくとも10年間位にわたって放置し、この間、何回も莫大なデーターを収集したものが基本となってまいりますが、まだ完全に確立されていないのが現状です。
(ベル研でも過去莫大なデーターを蓄積した筈ですが、世間にフィードバックされた物は極僅かであると思います)これは接触機構部品の特性上、止むを得ない事だと考えられます。なぜかといえば接触機構一つを取っても非常にセンシビティであるという事です。
たとえば銅板のガス腐食試験と接触抵抗の関係を測定しようとした場合、数時間のガス腐食試験でもかなりピークに近い様な値になってしまいますし、純銀のようなサンプルでも塩素ガスなどの試験でやはり数時間で高い値を示します。
金メッキサンプルなどは部分的に腐食が違う為、接触機構の評価はかなり複雑になってきます。それらのことから標準になるバラツキの無いサンプルを作るのは殆ど不可能に近い事ではないでしょうか。
事実99.9999%純金板の表面にも極僅かですが銅、銀の硫化物が観られ、接触抵抗の観点からみれば標準サンプルとして使うのは一考する必要があることがわかります。
また、これらの微妙な被膜を介在した接触抵抗評価も被膜を壊さないで測定できるかどうかなど数々のノウハウがあります。
これはある程度定量できるサンプルでの話なのですが、実際の製品になった場合、話は更に複雑になってきます。構造、材質、バラツキなどによりガス腐食の影響がかなり変わってくると思われますし、実際の部品では接触抵抗の変化を捕らえることはかなり難しくなってきます。
まず、気体濃度(H2S)と被膜の厚さと放置時間の関係を表すグラフですが、濃度が高いからそれに比例して膜厚が厚くなると思ってうては間違いです。それに低濃度でゆっくり出来た皮膜と高濃度で早く作られた被膜を接触抵抗で比較すると違いがあります。
それに単一ガスと複数の混合ガスではかなりの違いが表れます。
次は決められた金属片の前処理後の重量を高感度天秤で測定し腐食の重量変化を表すグラフ(2)を示しますが、試験サンプルの面積による違いはあるが、前処理、材料などの条件を充分検討すれば腐食試験のモニターとして使用可能かと思います。
ただし、塩類の生成を来たすような試験条件下などでは関連性がわかりにくくなる恐れがあります。
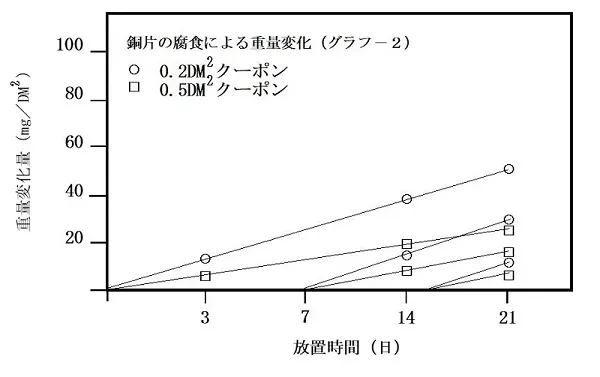 |
グラフ3は加速試験とフィールド試験との相関性を皮膜厚さで評価した結果です。
フィールドデーターはバラツキが当然大きく、原因として
1−場所による湿度の違い、2−大気中硫化水素濃度の違い、
3−温度のバラツキ、4−他の気体や塵埃などの混在、
5−試料表面の状態や初期表面の清浄度、6−試料の純度(Cu,Feの混在)、
7−光の当たる場所かどうかなどあげられる。
このデーターから0.01ppmの硫化水素濃度で湿度75%RHの条件をフィールドデーターと見なして
15ppmの硫化水素の加速試験との間で加速率をみると、次のようになる。
すなわち皮膜厚さを300Åとすると、15ppmH2Sでは 100時間かかり、0.01ppmでは1000時間かかるので、その比率は
単純に考えれば10しかなく、実際の部品ともなれば皮膜の破壊性が強い為、特に過酷な試験とはなり得ないのである。
最後に皮膜を殆ど破壊しない方法で混合ガスによる接触抵抗をとらえたデーターを最後のグラフ4に示します。
参考文献:接触技術の基礎と接触信頼性、向上と対策
御三重大学院 玉井 輝雄氏
Operation requirements for ccelerated gas testing using low concentrations
offlowing gas S A Harris ITT Cannon UK,Basingstoke |